Improving the vehicle checklist

20 April 2017
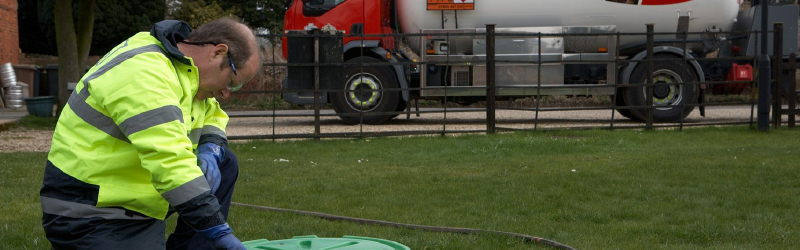
Improving the vehicle checklist
Technology’s impact on the logistics sector has been huge to say the least, but it will only continue to help businesses if it’s always evolving to meet their changing needs. That’s exactly why TouchStar is – and always will be - committed to improving its products.
This approach is demonstrated perfectly by the recent enhancements made to our vehicle checking system – an innovative tool designed to help organisations stay on top of their delivery vehicle fleets and maximise efficiency.
So what’s changed?
Check, and check again
Usually, vehicle checks are made once per outing – the driver goes through the list before embarking on their day’s journey. But what if a defect occurs or only shows during the employee’s shift? It could then go unnoticed for longer, leaving the driver and your cargo at risk.
Now, vehicle checks can be reperformed during the shift, making it possible to officially highlight concerns immediately or at least soon after they arise. You get more accurate and timely data, and your vehicles are kept in better shape.
More detail
A standard checklist requires your driver to check everything and show whether they’re satisfied or not as they go, but it may not always be a ‘yes’ or ‘no’ answer. Perhaps part of the vehicle is showing signs of wear that won’t cause issues straight away but could benefit from attention soon, or maybe the condition of a part isn’t immediately obvious.
The updated vehicle checking system allows users to configure the Vehicle Check process so that comments and observations can be captured during the driver’s rounds. This gives you the chance to keep a closer eye on your fleet.
Better time management
Vehicle checks will always take time if they’re done properly but there should be limits in place if you’re to keep productivity high. The latest improvements mean the start and completion times of each set of vehicle checks are captured and presented on the final PDF report.
With this information to hand, you can make sure your drivers are completing their checks efficiently – if they’re not, you can then address the issues quickly.
Accuracy where you need it most
A vehicle check is pointless if it’s not carried out properly – a driver could rush through the process or even be tempted to not do it at all if they’re pushed for time. The updated system combats this potential problem by registering when the driver’s TouchPC is removed from its cradle. This way, you have visibility of whether it was physically taken around the vehicle as the checks were performed.
Improved fault management
The data generated by your vehicle check system must be put to proper use if it’s to be a worthwhile investment, and that requires efficient organisation both during and after the checks are made.
Thankfully, the process can now be configured so that a defect number is captured for any fault raised by your driver. It’s also then possible to record a resolution type against that issue, so you and the relevant people within the business can monitor the process closely and accurately, ensuring the appropriate action has been taken. The result is a much smoother and faster-moving maintenance process, and more efficient vehicles.
If you think TouchStar’s constantly evolving vehicle inspection system could benefit your business, get in touch with us today.